Fertigungsprozesse produktiv gestalten
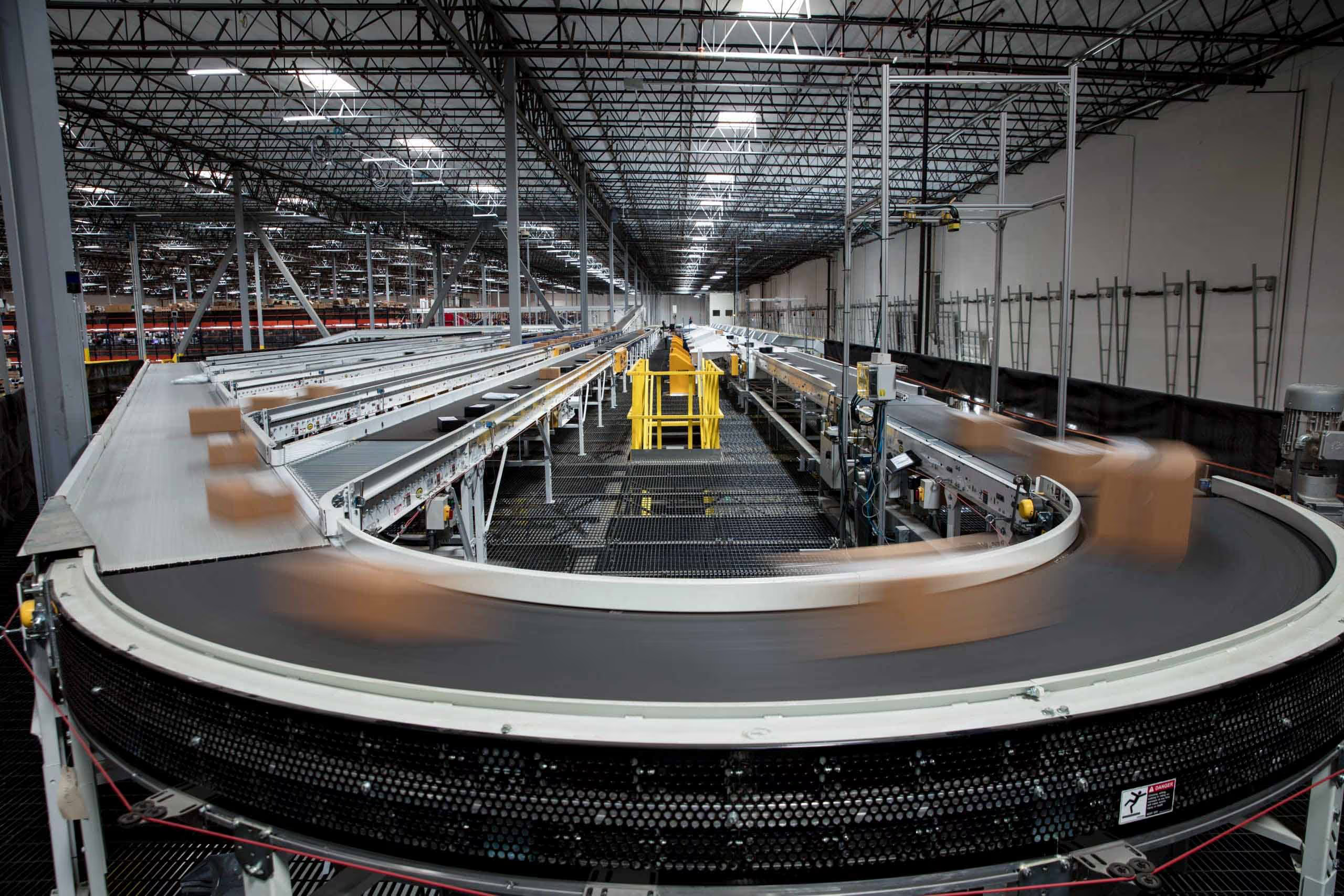
Was steckt hinter der Kennzahl OEE? Und wie können wir sie verbessern?
Die drei wichtigsten Erfolgsfaktoren in Herstellungsprozessen sind Leistung, Verfügbarkeit und Qualität. In diesem Blog-Beitrag erfahren Sie, wie Sie sich in allen drei Bereichen signifikant verbessern können. Soviel vorab: Der Schlüssel zur Effektivitäts-Steigerung liegt in den bereits verfügbaren Daten Ihres Unternehmens.
Betrachtet man Fertigungsprozesse aus der Vogelperspektive, gibt es drei Hauptfragen, deren Antworten über Erfolg oder Misserfolg entscheiden:
- Entspricht der Durchsatz Ihren Plänen?
- Können Sie die gewünschte Qualität liefern?
- Sind Ihre Anlagen verfügbar, wenn Sie sie benötigen?
Das OEE-Konzept
Wenn wir über diese Fragen sprechen, sprechen wir über eine der beliebtesten KPIs in der Fertigung: Der Overall Equipment Effectiveness (OEE) oder auf Deutsch „Gesamtanlageneffektivität“. Nehmen wir uns einen Moment Zeit, um uns mit dem zugrunde liegenden Konzept zu beschäftigen. OEE ist eine zusammengesetzte Kennzahl, die aus drei Komponenten besteht:
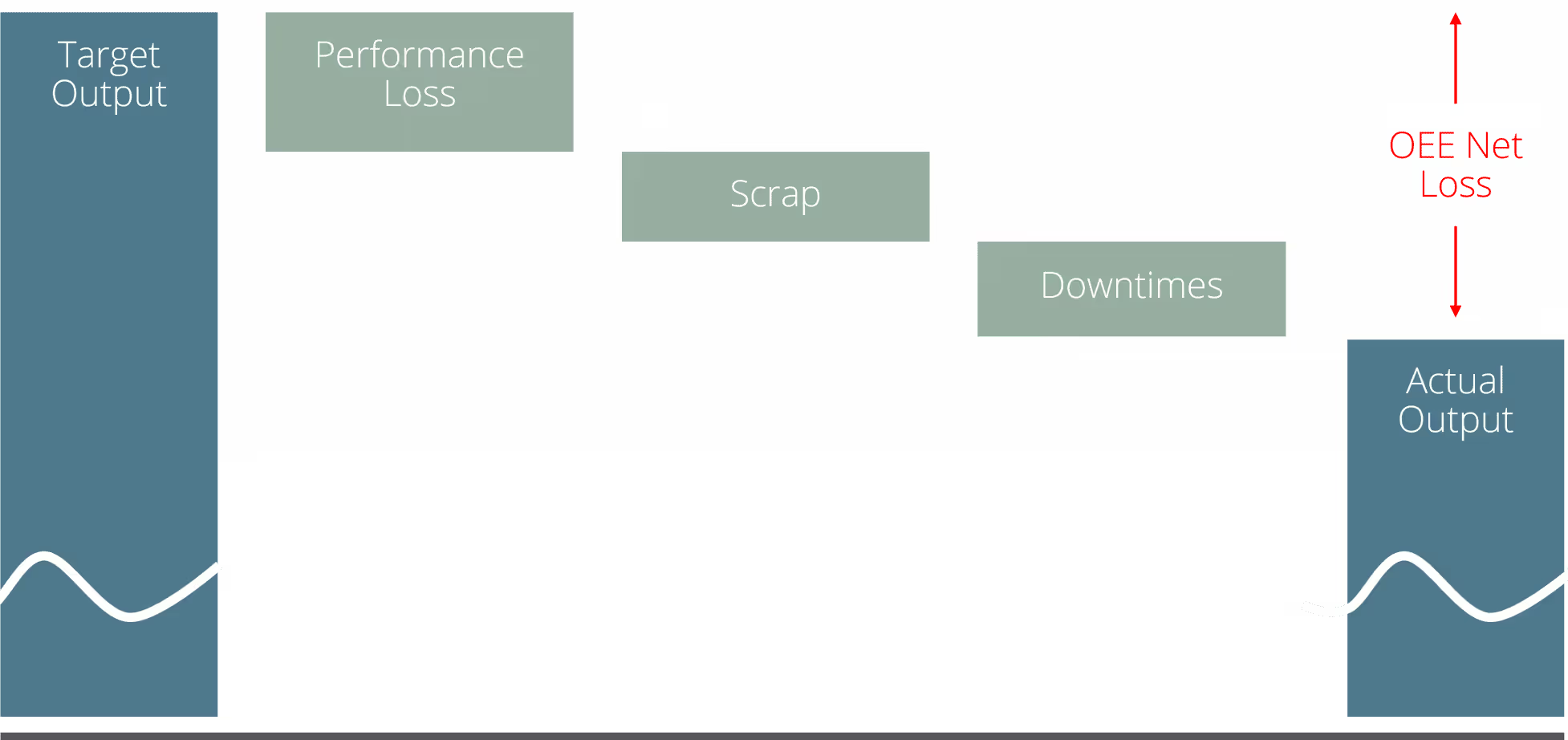
Verfügbarkeit: Die Nettolaufzeit einer bestimmten Anlage im Vergleich zu ihrer geplanten Laufzeit. Ungeplante Unterbrechungen wie technische Ausfälle oder Materialknappheit sowie geplante Stillstände, etwa Rüstzeiten/Werkzeugwechsel oder die tägliche Reinigung werden berücksichtigt. Beispiel: 20 Stunden geplante Produktionszeit pro Tag, 45 Minuten geplante Wartung und Reinigung und ein ungeplanter Stopp aufgrund technischer Probleme von 15 Minuten führen zu einer Verfügbarkeit von 19h / 20h = 95% Verfügbarkeit (eine Stunde Verlust)
Leistung: Hier dreht sich alles um Geschwindigkeit. Wir bestimmen die kürzeste theoretisch erreichbare Durchlaufzeit für ein Stück Fertigprodukt (= ideale Taktzeit) und multiplizieren diese mit der erreichten Stückzahl während eines bestimmten Zeitraums. Damit erhalten wir die theoretisch notwendige Laufzeit der Anlage. Diese dividieren wir durch die tatsächliche Nettolaufzeit im selben Zeitraum und erhalten einen Prozentwert für die Leistung. Beispiel: Bei einer idealen Taktzeit von 2 Minuten, 500 hergestellten Teilen und einer Nettolaufzeit von 18 Stunden wäre das Ergebnis (2 x 500) / 1080 = 92,6% (1,33 Stunden Verlust)
Qualität: Praktisch selbsterklärend: Wir teilen die Anzahl der Gutteile nach der Endkontrolle durch die Gesamtzahl der produzierten Teile und erhalten unseren dritten Prozentwert. Beispiel: 485 Stück haben die Endkontrolle bestanden, 500 Stück wurden hergestellt, daher liegt unser Qualitätsfaktor bei (485 Stück / 500 Stück) = 97% (15 Stück Verlust)
Diese drei soeben ermittelten Faktoren (oder Verlustraten, wenn man es andersherum betrachtet), kombinieren wir nun durch Multiplikation zu einem Gesamtwert:
OEE = 95% Verfügbarkeit x 92,6% Leistung x 97% Qualität = 85,33 %
Die perfekte Punktzahl von 100% ist so gut wie unmöglich zu erreichen. Was für Ihren Betrieb ein guter Wert ist, hängt stark von Ihrer Branche und verschiedenen Umgebungsparametern ab. Daher ist ein Benchmarking mit ähnlichen Unternehmen wahrscheinlich eine gute Idee. Mit den 85,33% in unserem Beispiel wären wir nach Meinung von Seiichi Nakajima, der TPM in den 1980er Jahren einführte, bereits „Weltklasse“. Für die meisten Unternehmen wäre dies also schon ein überaus ehrgeiziges Ziel.
Transparenz in der Supply Chain als Schlüssel zu mehr Performance
Die oben genannten OEE-Faktoren sind als nackte Zahlen erst einmal relativ bedeutungslos. Eventuell können Sie damit z.B. im Branchenvergleich grob abschätzen, wo Sie stehen. Für sich genommen – also ohne den Prozesskontext – sagen Ihnen diese Werte jedoch weder, wie gut Sie Ihr Potenzial nutzen, noch können Sie ableiten, wie oder wo Sie sich verbessern könnten. Dazu müssen Sie herausfinden, welche Parameter sich auf diese KPIs auswirken und wie Sie diese beeinflussen können. Hierzu braucht es vor allem erstmal aussagekräftige Daten und die passenden Werkzeuge, um daraus Erkenntnisse zu gewinnen und Maßnahmen abzuleiten.
Vier dieser Werkzeuge sind:
- Supply Chain Analytics
- Digital Twins
- S&OP Systeme
- Process Mining
Neue Einblicke durch Supply Chain Analytics
Die Basis möchte ich einmal unter dem Begriff Supply Chain Analytics zusammenfassen. Bereits einfache Analysen von Prozess- und Maschinendaten können dazu beitragen, die Gesamtanlageneffektivität zu verbessern. Neue Einblicke in die Leistung Ihrer Anlagen ermöglichen es, Schwachstellen zu identifizieren. Durch Sammeln und Auswerten von Daten zu Faktoren wie Produktionsraten, Stillstandzeiten und Qualitätsproblemen können Engpässe und Ineffizienzen in Ihren Prozessen erkannt werden. Diese Informationen können dann verwendet werden, um Anpassungen an Ihren Prozessen vorzunehmen, wie zum Beispiel die Durchführung von vorbeugenden Wartungsarbeiten oder die Optimierung von Produktionsplänen, um die OEE zu erhöhen. Darüber hinaus kann Supply Chain Analytics verwendet werden, um die Wirksamkeit dieser Anpassungen im Laufe der Zeit zu verfolgen und sicherzustellen, dass sie den gewünschten Effekt haben.
Auswirkungen simulieren mit Digital Twins
Ein digitaler Zwilling (Digital Twin) hingegen ist eine digitale Darstellung eines physischen Systems oder Prozesses, die es ermöglicht, die Leistung des realen Systems in Echtzeit zu simulieren und zu optimieren. Er kann dazu beitragen, die OEE zu verbessern, indem er die Möglichkeit bietet, die Leistung des realen Systems zu überwachen und zu analysieren, um Probleme frühzeitig zu erkennen und zu beheben. Zum Beispiel kann ein digitaler Zwilling von einer Produktionsanlage verwendet werden, um Daten zu sammeln und zu analysieren, um die Auslastung der Anlage zu optimieren, die Zuverlässigkeit zu verbessern und die Wartungszeiten zu verkürzen. Ein digitaler Zwilling kann auch verwendet werden, um die Auswirkungen von Änderungen an der Anlage vorab zu simulieren, um sicherzustellen, dass die Änderungen die gewünschte Wirkung haben, bevor sie in der realen Welt implementiert werden.
Bessere Koordination Dank S&OP
Unter S&OP (Sales and Operations Planning) versteht man einen Prozess, der die Geschäftspläne von Unternehmen in Einklang bringt und sicherstellt, dass Produktion und Materialbeschaffung mit den Verkaufsprognosen und der Nachfrage übereinstimmen. Indirekt kann diese integrierte Planung dazu beitragen, die OEE zu verbessern, indem die Produktionskapazitäten optimal auf die tatsächliche Nachfrage ausgerichtet werden. Ein gut funktionierendes S&OP-System kann dabei helfen, Überbestände, Engpässe und Rüstzeiten zu vermeiden, die zu erhöhten Ausfallzeiten und geringerer Produktivität führen. Weiterhin kann es die Koordination von Produktionszeiten und Lieferzeiten mit Kunden und Lieferanten erleichtern, was die OEE ebenfalls positiv beeinflussen kann. Ein S&OP-System kann auch dazu beitragen, die Produktionsprozesse zu optimieren, indem es Unternehmen ermöglicht, die Auswirkungen von Änderungen in der Nachfrage und der Produktionskapazität frühzeitig zu erkennen bzw. in verschiedenen Szenarien zu simulieren und darauf zu reagieren.
Prozesse optimieren mit Process Mining
Stehen sogar detaillierte Daten zu den einzelnen Prozessschritten in der Produktion zur Verfügung, bietet Process Mining Möglichkeiten, die deutlich über einfache Supply Chain Analysen hinausgehen. Mit der Process–Mining-Technologie analysieren Sie den digitalen Fußabdruck Ihrer Produktion. Entsprechende Tools verwenden Logs, also Protokolldateien verschiedener Quellsysteme wie ERP, Produktionsmanagement, Maschinen- und Gerätesteuerung usw. und übersetzen sie in eine visuelle Darstellung Ihres Prozesses. Vorausgesetzt, dass die Quell-Systeme miteinander verbunden sind oder sich zumindest einige gemeinsame Daten wie z.B. Auftragsnummern teilen, können Sie sogar angrenzende Prozesse wie das Kundenauftragsmanagement oder die (interne) Logistik einbeziehen, um beispielsweise Ausreißer des Verfügbarkeits-Faktors Ihrer OEE zu erklären. Die Visualisierung und Analyse der tatsächlichen Abläufe in Ihrer Fertigung liefert zu den nackten Zahlen also den Inhalt und hilft so nicht nur bei deren Interpretation, sondern zeigt auch direkt diejenigen Prozessschritte oder –abfolgen auf, die wahrscheinlich Probleme verursachen.
Fazit
Zusammenfassend lässt sich sagen, dass der Schlüssel zur Verbesserung der OEE vor allem in der Transparenz liegt. Neben unterschiedlichen Arten der Datenvisualisierung sind die Fähigkeiten, treffsicher Szenarien zu simulieren sowie nachvollziehbar und koordiniert zu planen, die wichtigsten Erfolgsfaktoren.
Moderne Lösungen für SCM-Analytics und S&OP bzw. Digital Twins eben hierfür den Weg. Der Einsatz von Process Mining kann darüber hinaus helfen, kritische Prozessabläufe oder Engpässe schnell zu identifizieren und im Sinne der OEE zu optimieren.