Next Level S&OP
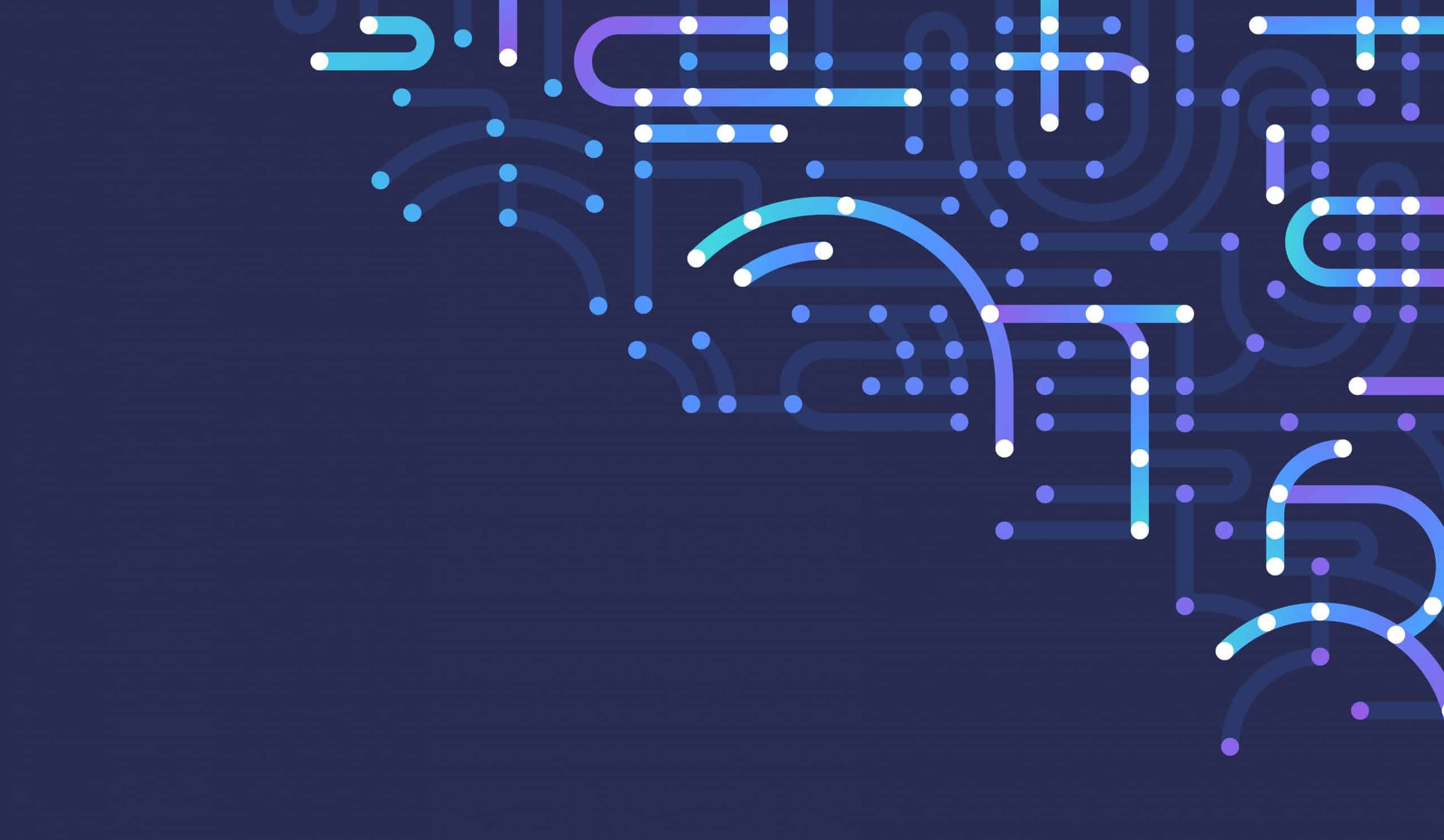
Bessere Planungsgenauigkeit dank integrierter Prozessanalyse
Wie Sie mit Process Mining die Qualität und Geschwindigkeit Ihrer Sales & Operationsplanung (S&OP) drastisch steigern können.
Um einen reibungslosen Ablauf in der Supply Chain eines Unternehmens sicherzustellen, müssen zahlreiche Abteilungen in enger Abstimmung stehen. Mit Silo-Denken und verstreuten Excel-Listen ist es jedoch schier unmöglich, die einzelnen Wertschöpfungsprozesse so zu vernetzen, dass alle Beteiligten die für Ihre Aufgaben erforderlichen Informationen haben. Mit schwerwiegenden Folgen: Es drohen Lieferschwierigkeiten, Kapazitätsengpässe und falsche oder zu hohe Lagerbestände.
Excel-Lösungen stoßen an ihre Grenzen
Der Planungsprozess mit dem größten Einfluss auf die Organisation und somit in produzierenden Unternehmen die „Mutter aller Planungen“ ist die Abstimmung zwischen Kundenbedarfs- und Produktionsplanung.
Dies beinhaltet:
- Sales Forecast (Bedarfsentwicklung, Kampagnen, Neuheiten, Ausläufer, Neukunden)
- Produktionsseitige Abbildung des Bedarfs (Arbeitspläne, Stücklisten, Kapazitäten, Materiallogistik)
- Abgestimmter Supply-Plan einschließlich Kapazitätsanpassungen, optimalen Losgrößen und Lagerkennzahlen
- Analyse finanzieller Auswirkungen der abgestimmten Pläne auf GuV und Bilanz
Häufig werden diese einzelnen Teilplanungen nicht nur von verschiedenen Personen, sondern auch in verschiedenen Systemen durchgeführt. Nachfrage und Angebot miteinander in Einklang zu bringen und einen vernetzten Plan über die Gesamtorganisation zu erstellen, ist entsprechend mit einem enormen Abstimmungsaufwand verbunden und daher wirklich sinnvoll nur mit Hilfe eines integrierten Planungstools zu lösen. Ist-Daten-Analysen, Prognose-Algorithmen, Work-Flow-Steuerung und Add-Ons wie HR-Planungsmodule oder die automatische Erstellung von GuV, Bilanz und Cash-Flow auf Grundlage der Plan-Daten runden das Paket ab.
Basisparameter für eine funktionierende S&OP-Planung sind Annahmen z.B. über Kapazitäten, Bearbeitungszeiten und Verfügbarkeiten. Diese Annahmen sind entweder komplett theoretischer Natur oder werden sporadisch durch manuelle Messungen oder Kapazitätsauswertungen ermittelt. Ob ein Team oder eine Maschine in der Lage ist, 80 Fertigteile pro Stunde zu produzieren oder vielleicht doch eher 100, macht nicht nur für die tatsächliche Auftragsbearbeitung einen großen Unterschied. Wird diese Zahl als Eingangsparameter für die toolgestützte Planung verwendet, weicht das Planungsergebnis eventuell stark von der Realität ab. So besteht die Gefahr, dass der Vertriebs-Forecast reduziert werden muss oder aber umgekehrt Produktionsanlagen nicht gut ausgelastet werden, weil man von einer zu geringen Produktionskapazität ausgeht. Process Mining auf Grundlage von ohnehin im Unternehmen vorhandenen Prozess- bzw. Log-Daten schließt diese Lücke und ersetzt Vermutungen durch belastbare Kennzahlen.
Fazit
Die Einbindung von Process Mining in die Planung ermöglicht es, diese meist theoretischen Annahmen durch die laufende Analyse der zugrundeliegenden operativen Prozesse zu verifizieren und korrigieren. Statt sporadischer Messungen wird die Performance innerhalb eines Prozesses kontinuierlich überwacht. Prozess-Störungen, Bottlenecks und Trends in den Durchlaufzeiten werden sichtbar und können durch Daten-Integration von Process Mining- und Planungsdaten direkt berücksichtigt werden. Doch nicht nur das: Entspricht das Planungsergebnis nicht den Erwartungen, liefert Process Mining die Gründe für beispielsweise eine überraschende Unterdeckung bei einem konkreten Produkt. So lassen sich noch während der laufenden Planungsrunde nahezu in Echtzeit Störungen oder Abweichungen vom Soll-Prozess im Detail identifizieren und Maßnahmen ableiten, um diese zu beseitigen. Näher an der Wirklichkeit war Planung noch nie.