Agile project approach in 100% remote work
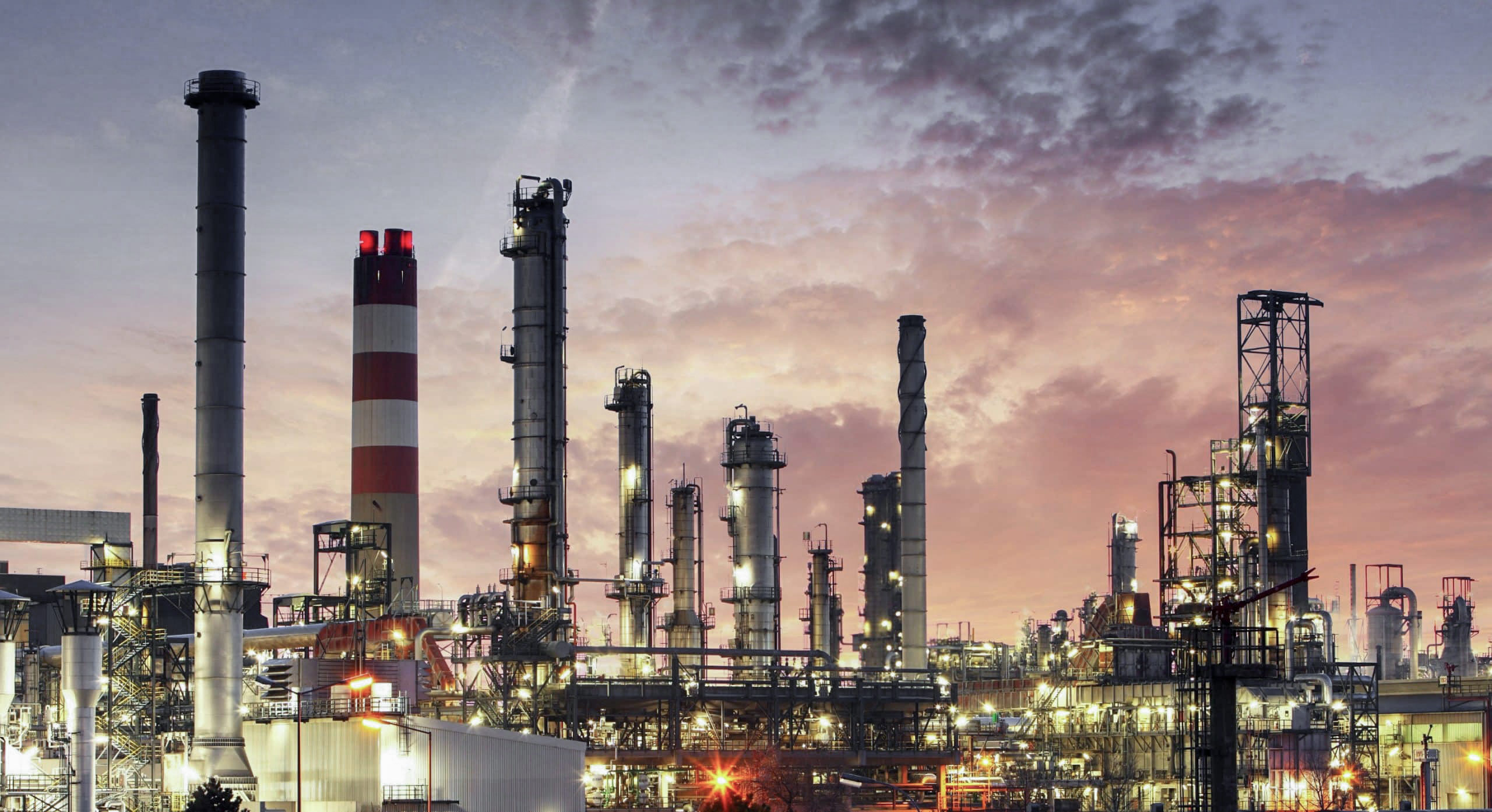
How Aurubis and celver successfully implemented an SCM planning platform remotely
Agile projects in supply chain planning thrive on mapping individual processes and, above all, on direct and close cooperation with the customer. Aurubis AG is a leading global supplier of non-ferrous metals and one of the largest copper recyclers in the world. At the beginning of 2020, Aurubis decided to migrate the planning processes in the supply chain to a standardized platform as part of the APS program and started the project "Purchasing and Production Planning in the Copper Blister & Scrap Division". The goal of the program is to reduce error-prone manual input processes and create scenario analyses in procurement planning. In the long term, Aurubis wants to be able to use the program to plan more details at a higher frequency, resulting in better predictability. In April, Aurubis decided to start the first planning project with the planning specialist of celver AG and the BOARD platform.
COVID-19, however, made it necessary for the entire project to be carried out 100% remotely from the home office, from the visual specification of the planning processes, implementation, staff training to go-live support.This is not without a certain irony, as the Aurubis and celver sites are just a stone's throw away from each other in Hamburg. "Certainly, our experience with online tools such as Teams, Sharepoint and JIRA helped us to create the right space for the project," says Klaus Henning Wenck. "Supported by the agile project and implementation methodology using Scrum as well as the close, daily collaboration, we were thus able to make up for the spatial separation." In retrospect, some learning effects during the project phase were also important. Above all, the shortening of the sprint runs from the original four weeks to two weeks, continuous testing, and close communication and clarification of expectations with the other stakeholders helped to stay on "time & budget" in the project. "This is not the case in every IT project," says Klaus Henning Wenck with a slight smile. "So not only did we run a good project, we also ran one under special circumstances".
The benefit of the planning solution is immediately apparent in the weekly P&OP meeting. The data is now available from automated sources and without manual preparation. As a result, the individual planning managers at the sites have more time and can focus on data quality, commenting and the forecast. This enables the person responsible for planning to react much faster to the P&OP process - based on the aggregated information - and to use simulation to prepare and conduct the weekly coordination meetings directly in the software. Klaus Henning Wenck comments: "After the experiences of the first project, we will now directly enter the upcoming sub-projects with celver AG to further optimize our planning processes in the supply chain. The very cooperative and successful collaboration with celver AG makes us very confident in this regard".
Even before COVID-19, we were able to carry out large parts of our projects remotely together with our customers with a view to efficient realization. But "the new normal" with a restriction of on-site activities has caused a rethinking in realization. Modern, cloud-based infrastructures as well as new methodological competencies and procedures, among others in the design of focused, creative workshops, have led to a 100% successful remote implementation of the entire project. Nevertheless, we are looking forward to on-site activities and the direct exchange with our customers again in the future.